در یک کارخانه فولادسازی، مهمترین و اصلیترین مواد اولیه تولید فولاد مواردی همچون سنگ آهن، زغال سنگ، سنگ آهک و آهن قراضه هستند. دو روش اصلی و مهمی که توسط آن فولادسازی صورت میگیرد، روش کوره بلند و روش کوره قوس الکتریکی میباشد.
در ادامه این مقاله قصد داریم به شرح چگونگی انجام روشهای تولید، بررسی مواد اولیه تولید فولاد و تاریخچه آن بپردازیم. با شاهین فلز سپاهان همراه باشید.
مواد اولیه چیست؟
هر محصول نهایی برای تولید نیازمند مواد مورد نظر خود میباشد. در واقع ماده خام یا ماده اولیه که به انگلیسی Raw material نامیده می شود و یا با عنوان ماده فرآروی نشده یا ماده اساسی نیز شناخته می شود، ماهیت و متریال اصلی برای تولید کالاها و محصولات نهایی را تشکیل می دهد.
در این مطلب قصد داریم به طور اختصاصی به توضیح مواد اولیه فولاد و روش تولید آن بپردازیم.
مواد اولیه فولاد
همانطور که اشاره کردیم برای تولید هر محصولی به مواد اولیه و اساسی آن نیاز است. فولاد ماده ای است که امروزه از محصولات نهایی تولید شده با آن در صنایع مختلفی استفاده می شود. آهن قراضه و آهن اسفنجی، دو ماده اولیه اساسی تولید فولاد در کوره می باشند.
در ادامه بهتر است با مواد اولیه چند محصول مرتبط با فولاد آشنا شوید و در ادامه صرفا به تاریخچه و پروسه فولادی سازی اشاره خواهیم کرد.
مواد اولیه فلزات چیست؟
به طور کلی می توان گفت مواد اولیه تولید فلزات شامل موارد زیر می شود:
- مواد ریخته گری
- فلز شکل گرفته و منبسط شده
- سخت افزار
- فلز مقطعی
- فلز تخت
- سیم جوشکاری
مواد اولیه آهن چیست؟
سنگ آهن تحت فرآیندهای متفاوتی به فولاد تبدیل میگردد و مورد استفاده قرار میگیرد. در واقع می توان گفت فولاد، آهن و چدن از مشتقات سنگ آهن به حساب میآیند پس ماده اولیه و اصلی تمامی این محصولات، سنگ آهن است.
تاریخچه تولید فولاد
گریدهای مختلفی از فولاد وجود دارد. بسیاری از آنها در دو دسته فولاد کربنی و آلیاژهای فولاد تقسیمبندی میشوند. بالغ بر 100 سال پیش، ساخت آلیاژهای فولاد آغاز شد و امروزه 10 درصد از کل فولاد تولیدی را شامل میشود.
فولاد کربنی چیزی درحدود 0.1 تا 1 درصد کربن و مقادیر پایینی از عناصر منگنز و سیلیسیم را دارا است. کربن موجود در فولاد در عین آنکه مقاومت فولاد را افزایش میدهد، منجر به کاهش چکشخواری میشود. افزون بر آن، وجود کربن امکان ایجاد بعضی از ویژگیهایی که برای عملیات حرارتی همچون آنیلینگ، نرمال سازی، آبدهی و غیره مناسب هستند را فراهم میسازد.
این عملیات، منجر به تغییر ریزساختار فولاد میشود. وجود کربن در ساختار فولاد برای اولین بار، اواخر قرن 18 میلادی کشف شد. تا 100 سال بعد، توسعه دانش متالورژی تا آنجایی ادامه پیدا کرد که امکان همبسته کردن عملیات حرارتی و ویژگیهای مکانیکی با میکروساختار فولادها به وجود آمد.
به همین علت امکان به دست آوردن محدودهای از ویژگیهای مکانیکی در یک درصد کربن مشخص، فراهم شد. اوایل برای تولید فولاد، تکنیکهایی برای تولید فولاد کربنی در مقادیر پایین به کار گرفته میشد. علاوه بر آن عملیات حرارتی به صورت آزمایشی و بدون برخورداری دانشی از آن، انجام میشد. با توجه به شواهد موجود، هندوستان در این زمینه شروع کننده بود و در حقیقت هندوستان، فولاد را به تمام دنیا صادر کرد. کشورهای عراق، سوریه و ژاپن از هزاران سال قبل، در این زمینه دانشهایی به دست آوردند و اروپا نیز از قرون وسطی، شروع به تولید فولاد کرد.
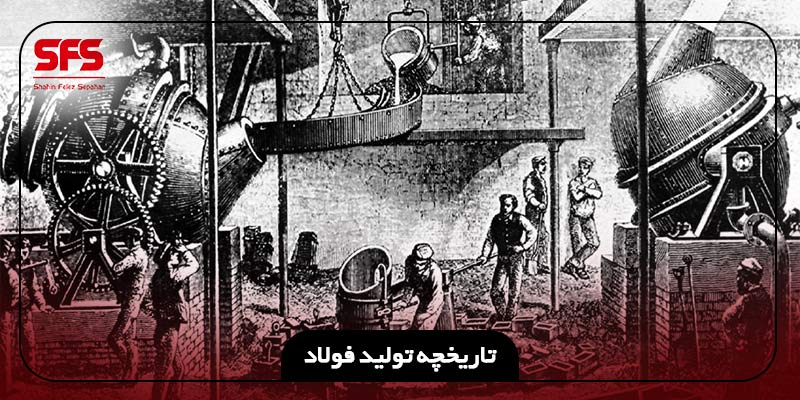
اولین فرآیندهای تولید فولاد، به گرم کردن آهن در حضور مواد حاوی کربن در کورههای سرپوشیده برمیگردد. همین امر منجر به آن شد که آهن با جذب کربن به فولاد تبدیل گردد. هنگامی که آهنسازان در اروپا موفق به تولید آهن مذاب شدند، آهن کار شده را با خالص سازی مذاب آهن به وجود آوردند.
سپس آن را به همراه مواد کربنی در کورههای بسته، به فولاد تبدیل کردند. این فرآیند که با عنوان سمانته شدن نیز شناخته میشود، با مقادیر مناسبی از کربن، نقطه ذوب فولاد کاهش پیدا میکند و ذوب آن تسهیل میشود.
نحوه تولید فولاد یا پروسه فولادسازی چگونه انجام میشود؟
در کوره، آهن قراضه و آهن اسفنجی مواد اولیه تولید فولاد هستند. در کوره مقداری آهن قراضه شارژ میشود و به کمک ایجاد قوس الکتریکی ذوب میشوند و پس از آن آهن اسفنجی را در کوره شارژ میکنند.
همه چیز درباره آهن اسفنجی در مقاله آهن اسفنجی چیست + روش تولید و 7 مزیت آهن اسفنجی
خواص فیزیکی آهن قراضه اثر مهمی داشته و در صورتی که انتخاب درستی صورت گیرد، منجر به شکستن الکترود، سرریز شدن فولاد مذاب و یا حتی انفجار میگردد. برای به حداقل رساندن مشکلات و بهینهسازی عملیات، انواع آهن قراضه مورد استفاده قرار میگیرد.
افزون بر مواد اولیه آهندار که تشکیلدهنده بخش اصلی شارژ کورههای قوس الکتریکی هستند، مواد دیگری به عنوان کمک ذوب، سربارهزا، روانساز یا موادی برای آلیاژ کردن و یا تصحیح ترکیب نهایی مذاب موردنیاز هستند. در بعضی موارد عنصر کربن نیز برای تنظیم آنالیز نهایی ذوب مورد نیاز است. آهک که یکی از مهمترین انواع کمک ذوب میباشد، برای تشکیل سربارهها و اثر گذاشتن بر واکنشهای شیمیایی در مراحل مختلف تصفیه متالورژیکی به کوره اضافه میشود. عناصر آلیاژکننده که غالبا مواد فلزی هستند، برای رسیدن به ترکیب نهایی موردنظر، به کوره افزوده میشوند.
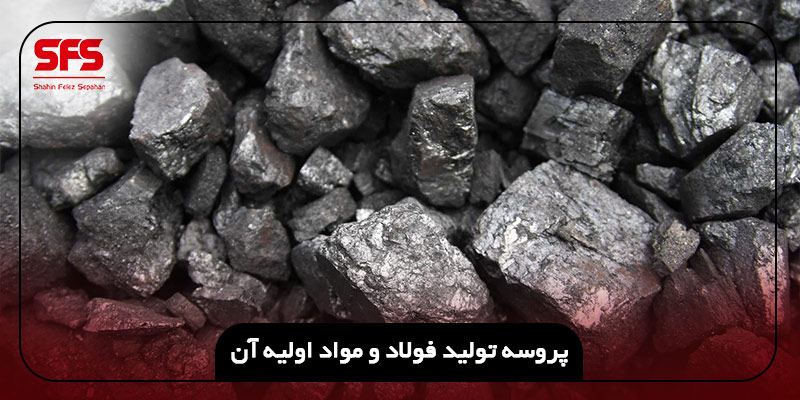
هنگامی که مواد، از مقادیر بالای عناصر آلیاژی برخوردار باشند، فروآلیاژ نامیده میشوند. افزون بر آن، موادی همچون فرومنگنزهای کم کربن و پر کربن و فروسیلیکو منگنز و فروسیلیسیم و دیگر فروآلیاژها اضافه میگردند. برای ازدیاد کربن میتوان به صورت مستقیم کربن را وارد کوره نمود.
مواد اولیه تولید فولاد چیست و روش های تولید آن کدام است؟
آیا میدانید مواد اولیه ذوب آهن چیست؟ برای ساخت فولاد، دو روش اصلی وجود دارد. روش اول استفاده از آهن اسفنجی و کورههای قوس الکتریکی یا EAF برای ذوب آهن اسفنجی و پس از آن آلیاژسازی است.
در این روش مواد اولیه در داخل یک کوره الکتریکی شارژ شده (آهن قراضه اولیه و یا آهن احیای مستقیم (آهن اسفنجی) و الکتریسته) و به طور میانگین، میزان مصرف آهن قراضه 1050 کیلوگرم، زغال سنگ 65 کیلوگرم و 43 کیلوگرم برای تولید یک تن فولاد خام میباشد.
روش دوم استفاده از آهن خام (آهن تولید شده در فرآیند احیای غیرمستقیم) و سوزاندن کربن اضافی آن در کوره بلند است. طی این فرآیند میزان کربن آهن خام از بازه 5.3 تا 6 به 2 تا 1.5 درصد وزنی کاهش پیدا میکند. درنهایت عناصر دیگر در آن افزوده میشوند تا ترکیب مورد نظر بدست آید. در این روش به صورت حدودی مقدار 1725 کیلوگرم سنگ آهن، 645 کیلوگرم زغال سنگ، 150 کیلوگرم سنگ آهک و 138 کیلوگرم آهن قراضه برای تولید یک تن فولاد خام، مورد استفاده قرار میگیرد.
در مقاله سنگ آهن چیست + نحوه استخراج و 7 کاربرد سنگ آهن درباره سنگ آهن بیشتر بخوانید.
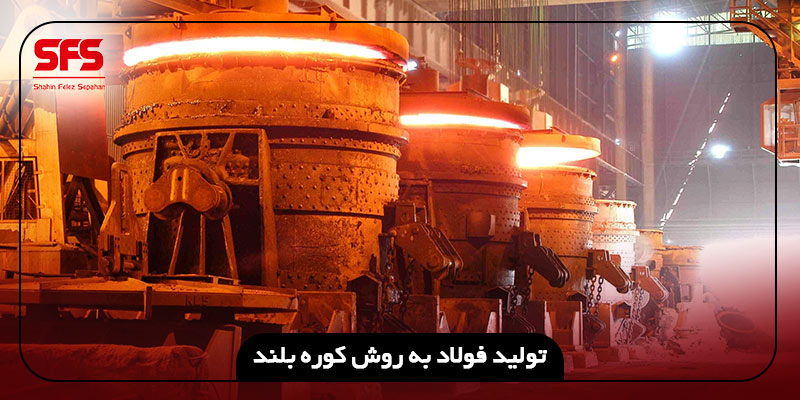
آهن معمولا به صورت سنگ معدنی مانند مگنتیت و هماتیت در پوسته زمین یافت میشود. فولاد را با سوزاندن کربن آهن خام سفید و همجوش کردن آن با کمی کربن و اندازه کردن عنصرهای دیگر در آن، به دو روش خمیری کردن و ذوب کردن تولید میکنند.
مواد اولیه ذوب آهن چیست؟
شاید برای شما این سوال پیش آمده باشد که مواد اولیه ذوب آهن چیست!؟ در واقع، آهن از ذوب سنگ آهن در کورههای ذوب آهن، حاصل میشود.
استاندارد سازی فولاد
فولادهای متداول از کربن با درصد وزنی حدود چند هزارم درصد تا یک درصد برخوردار هستند. همچنین تمامی فولادها مقادیر متغیری از عناصر دیگر بهویژه منگنز را دارا میباشند. منگنز علاوه بر کاهش اکسیژن مذاب، توانایی کار گرم فولاد را نیز بهبود میبخشد و منجر به افزایش آن میگردد.
سیلیسیم، فسفر و سولفور نیز در اندازههای کوچک وجود دارند. امکان بودن مواد دیگر نیز در مقادیر بسیار کم به علت طبیعت فرآیند تولید فولاد یا ایجاد خواص مطلوب وجود دارد. فولاد میتواند به صورت ریخته یا شمش تولید گردد و یا میتوان با گرم کردن مجدد، بر روی آن با استفاده از یکی از روشهای نورد، اکستروژن، فورج یا دیگر روشهای دیگر تولید شکل داده شود. برای کاربردهای مهندسی فولادهای شکل داده شده، با داشتن فرم، کیفیت سطحی، استحکام و دمای کاری متنوع، بیشترین کاربری را دارا هستند.
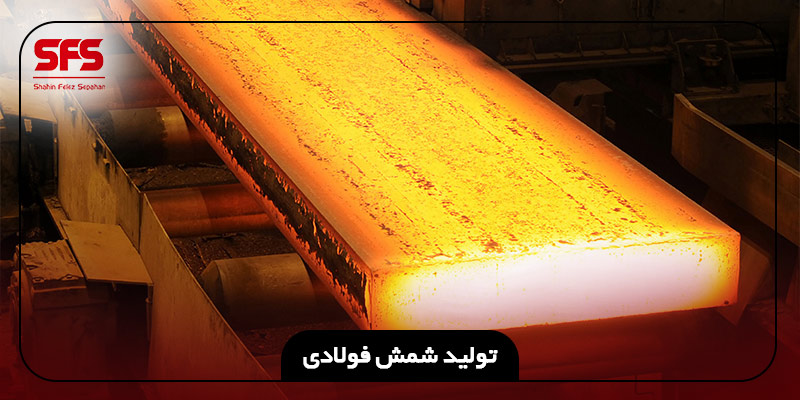
کاربرد انواع مختلف فولاد چیست؟
فولاد در صورتی که تا 0.2 درصد کربن داشته باشد، در ساختن سیم، لوله و ورق فولاد مورد استفاده قرار میگیرد. فولاد متوسط 0.2 تا 0.6 کربن داشته و در ساخت ریل، دیگ بخار و قطعات ساختمانی استفاده میشود.
درصورتیکه میزان کربن فولاد 0.6 تا 1.5 درصد باشد، فولاد سخت خواهد بود و در تولید ابزارآلات، فنر، لوازم آشپزخانه همچون کارد و چنگال، کاربرد دارد. از آنجایی که بعضی از فولادها در برابر دما و حرارت بالا، از خود مقاومت بسیاری نشان میدهند، از آنها در ساخت انواع مخزن و لوله در پالایشگاهها و کارخانهها، استفاده میگردد.
جمع بندی
در محتوایی که به آن پرداختیم، مواد اولیه تولید فولاد، روشهای تولید و تاریخچه تولید آن بررسی شد. فولاد، به دو روش کوره قوس الکتریکی و کوره بلند تولید میشود. از انواع مختلف فولاد با درصد سختیهای گوناگون در تولید لوازم خانگی، پالایشگاهها و کارخانهها استفاده میشود.
سوالات متداول:
مواد اولیه گندله سازی چیست؟
گندله یکی از فرآوردههای آهن و از اشکال سنگ آهن است و از نرمه سنگ آهن و سایر مواد افزودنی تولید میگردد.
مواد اولیه تولید شمش فولادی چیست؟
مواد اولیه برای تولید شمش فولاد همچون دیگر مقاطع فولادی، سنگ آهن میباشد.